As a pressure pipeline component, the pipeline ball valve bears not only the pressure of the medium but also the pressure caused by its uncertain factors, such as the bending load caused by unbalanced ground subsidence, mountain landslide, debris flow, earthquake, etc., as well as the change of the tensile and extrusion load of materials caused by the change of day and night and seasonal temperature. The valve stem is mainly used to transmit the opening and closing power and is the main transmission element of the opening and closing ball valve. The main function of the ball valve is to cut off or connect the fluid channel in the pipeline. The valve seat is one of the important parts of the ball valve. When the ball valve is closed, it prevents the medium from flowing from upstream to cavity and from cavity to downstream. Through the medium force or spring force, the valve seat and the ball establish sealing pressure to form a seal. Valve stem seal is also very important. In order to prevent the medium from leaking through the valve stem seal, it will be an important research topic. For flammable, explosive and combustible media, leakage will directly lead to accidents, so the reliability of valve stem seal will be studied emphatically.
Reasons for Sealing Principle and Leakage
1. Analysis of sealing principle of valve stem packing
There are two types of valve stem seals: packing seal and bellows seal, and the seasoning seal is the most commonly used. The packing seal includes flexible packing and another packing which generates an axial force of packing through the gland. The most commonly used materials are graphite and plastic, metal and carbon fiber. Sealing forms mainly include rotary sealing and reciprocating sealing. The most common materials are asbestos packing, PTFE woven packing, rubber O-ring and plastic molding packing. During the opening and closing of the valve stem, the inner hole of the stuffing box will be worn, resulting in clearance and valve leakage. The valve stem should have proper hardness and elasticity, be resistant to medium erosion and abrasion, and have excellent machinability. In addition, in order to increase wear resistance and corrosion resistance, the valve stem needs surface treatment to avoid medium leakage caused by valve stem bending, corrosion and surface tension. The valve stem seal is a low-speed and frequent-action seal, and its own system consists of several components. It promotes the axial preload of the gland by loading bolt torque or gland preload, and it is a kind of balance between the compression deformation of packing and the movement torque of the valve stem. When the packing in the stuffing box is squeezed axially by an external force, the packing will deform greatly in the radial direction, thus sealing the valve stem. Due to the microscopic roughness difference of the valve stem surface, the contact degree between the packing and the valve stem surface is inconsistent, and the contact part reaches a limited lubrication state. A small oil groove is formed through the non-contact groove, and the oil groove is thick. When the packing in the stuffing box is axially extruded by the packing, the high plasticity of the packing makes it form radial residual extrusion stress and tightly contact with the bearing surface. At the same time, add lubricating oil into the filler. When the lubricating oil is squeezed, a lubricating oil layer will be formed between the mating surfaces. Because of the unbalanced contact state, the contact part becomes boundary lubrication, and the non-contact groove becomes a small oil groove with a thick oil film. When moving with the important official packing, it becomes an irregular labyrinth between the contact part and the non-contact part, which has the function of preventing the liquid from flowing and leaking. The radial pressure distribution and average pressure distribution of packing are that the radial pressure increases exponentially from inside to outside, and the average pressure decreases exponentially from inside to outside. The sealing packing can be partially sealed outside and the compression force of 2 to 3 packing rings close to the radial direction of the gland is the highest.
2. Causes of packing leakage
1) incorrect selection of filling materials
Packing can be used to supplement the gap of the ball valve stuffing box, so as to prevent the medium from leaking when passing between the valve stem and the stuffing box gap. Packing should have the advantages of good sealing, low friction, less corrosion, good elasticity and plasticity, certain hardness and high chemical stability. The valve stem sealing ring mostly uses packing sealing technology, which is a dynamic closed structure. Packing is filled between the valve stem and the stuffing box to prevent the medium from escaping. The main factors that cause sealing leakage of packing are: packing does not meet the requirements, packing configuration is not appropriate, packing is easy to be aged or damaged, etc. If the filler is not properly selected, it will easily cause leakage, and it will not be resistant to medium corrosion, high pressure or vacuum, heat and so on. And it's not the right size. If the packing is too thin, it is under pressure.
When the cover is tightened, the radial deformation force generated by the packing is insufficient, and the ideal sealing effect cannot be achieved. Poor storage of materials or beyond the shelf life. If the storage is poor or over time, the packing may be aged, broken or lack toughness, so the expected sealing effect cannot be obtained. Packing should be selected according to the type of gland and the pressure, high temperature and corrosion resistance of the medium.
2) Packing is not installed correctly.
A reasonable packing arrangement is an important link to ensure that the valve does not "run or leak". If the arrangement is unreasonable, it will cause air leakage when the valve stem is sealed. The lid won't press tightly. However, only when the packing bears appropriate residual compressive stress, can it form appropriate radial deformation, thus filling the gap between the valve stem and the inner wall of the packing box, and achieving good sealing performance. However, if the balance pressing force is not enough, the radial deformation capacity of the packing is insufficient, and the sealing effect will be poor. The determination of pressure is related to factors such as equilibrium pressure. If the packing area is too small, there is no close connection with the packing section. If the cutting and arrangement of the filling cut are not proper, the included angle of the filling cut should not be too large or too small, and the included angle of the filling cut should be about 30 or 45; The overlapping angle of each ring cutting seam must be staggered by 120 so that the sealing effect is good, but the number of packing installation layers is not enough. If the packing arrangement is not sufficient, the gland can't press the packing tightly, so effective sealing can't be realized; Multi-layer packing, multi-layer continuous packing, single-piece compaction, uneven packing surface of the stuffing box, small cracks, easy to tighten and cause leakage, tightening and loosening will also lead to packing seal leakage. Poor quality packing, in a short period of time, will cause great wear and tear near the packing. The filling time is too long. The packing will be damaged, rusted, aged, dried, etc. after a long time of use, and gradually lose its compactness, resulting in seal leakage, which is common in packing sealing.
Optimization measures for sealing packing
The main factor in valve stem leakage is the choice of valve stem material. Because the main function of the valve stem is to adjust the opening and closing of the ball valve, it will cause more material damage, resulting in valve stem leakage; However, if the material is poor, the damage will be very serious when used frequently, so it will cause the leakage of the medium or affect the normal opening and closing of the ball valve, resulting in a large range of medium loss. In order to overcome this problem, we must start with the corrosiveness of the medium, and apply all kinds of valve stem materials to different media. The usual methods include selecting appropriate materials and processing surfaces. The surface treatment of valve stem is usually surface heat treatment, although these methods can better improve the surface wear resistance of valve stem, the cost often exceeds the budget.
1. Optimization of packing sealing structure
The traditional valve stem sealing method is usually used for compressed packing, which mainly refers to the soft material pressed into the packing box to protect the valve stem. By pre-tightening the gland, the packing expands radially, and the transmission pressure decreases in turn. The pressure exerted on the end of the gasket also forms the same pressure on the side support surface. If the packing has been compacted, and the lateral pressure capacity of the packing is usually higher than the medium pressure by a pressure value applied to the packing, a certain sealing effect will be produced spontaneously. However, the traditional packing lateral expansion pressure regulation performance is not good, and the damage to the valve stem is also very serious. Therefore, in order to improve the tightness of the packing, the radial pressure formed by the packing at the bottom of the packing box on the valve stem should be higher than the medium pressure. When designing the packing seal, it is necessary to generate a large lateral pressure and be able to meet the requirements of continuous adjustment, and the axial force can be adjusted without changing the packing, so as to ensure that the sealing performance is greatly improved. The ideal sealing effect is that the packing has large compression deformation, a high rebound rate, and good sealing performance at the valve stem. Therefore, applying a small force to the packing can effectively realize the tight fit between the packing and the valve stem. Using H-ring (Figure 1, Figure 2) solves the valve stem sealing well.
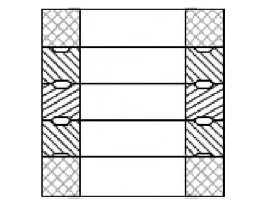
Fig. 1 H-ring with pressure below 900 LB
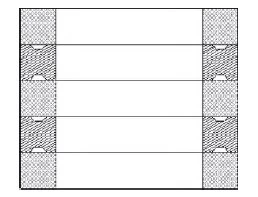
Fig. 2 High pressure contains H-ring over 900 LB
2. Apply pre-tightening force optimization
The valve is prone to packing damage after the long-term operation, resulting in insufficient sealing pressure and leakage. At the same time, when the system fluctuates due to water temperature, air pressure, etc. in the environment where the system is heated up and used, the pre-tightening pressure and holding pressure of the bolt connection will change constantly due to the different degrees of thermal expansion. The pre-tightening force exerted by bolts on the packing will be attenuated layer by layer from top to bottom, which is easy to cause the packing in the upper part close to the gland to deform greatly and lock up, while the packing in the middle and lower part will deform less and the sealing effect will be poor. It's easy to have a large initial torque. After a period of operation, the sealing effect of the packing and valve stem will be weakened, which is easy to cause leakage. The usual method is to continuously apply large pre-tightening pressure to the packing while ignoring the adverse effect of over-tightening on packing sealing. Increasing pre-tightening will speed up the wear of the contact between seasoning and valve stem, thus reducing the service life of seasoning. Therefore, to improve the tightness of valve stem packing, it is only necessary to apply proper pre-tightening pressure to the packing.
The structural design is optimized so that the main sealing ring and the front and rear end rings are uniformly stressed, and the stress and deformation of the sealing rings of each layer are treated differently by processing technology. In this way, the bolt exerts a pre-tightening force on the packing gland, and the force attenuates layer by layer, and the deformation of each layer of packing is differentiated (that is, the same deformation of each layer of packing can be achieved by different forces), which solves the valve stem leakage well and achieves a good sealing effect. In order to ensure the reasonable pre-tightening force of the packing, the gland or bolt can be pre-tightened according to the total pressure of FYT packing, so as to stabilize the pre-tightening force in long-term work. Maintaining the radial compression of the packing in a reasonable range can automatically compensate for the packing damage, thus having the function of avoiding insufficient or excessive pre-tightening, thus increasing the sealing life of the packing. Generally speaking, there are two kinds of spring compensation methods for stem packing seals: cylindrical helical spring and disc spring.
3. Installation optimization of valve stem packing
Before installation, clean the stuffing box and check the valve stem. The fitting tolerance of packing and valve seal installation refers to all clauses of API622 standard 4.1.1. The roughness of the valve stem is ≤ 0.8μ m, and straightness is ≤ 0.04mm per 305mm; According to the depth of the filler culvert, calculate the number of filler composite rings; The total height of the packing group is ≤ 20mm, and the cross-section is ≤ 5mm. It can be assembled into the packing culvert in one piece, and the bolt pre-tightening is repeated three times. The total height of the packing group is > 20 mm, and the cross-section is > 5 mm. In order to ensure the low dissipation effect, H-shaped ring packing is used. First, the packing is placed in the packing box layer by layer (five layers), then the valve stem is put on, and a certain torque is applied through the packing gland bolt to compress the packing, with the compression degree of 80%-65%, and the torque value at this time is recorded. Then, loosen the packing gland bolt and install a layer of packing.
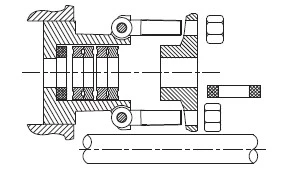
Figure 3 Packing Installation Step 1
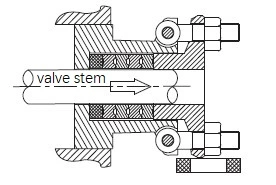
Figure 4 Packing Installation Step 2
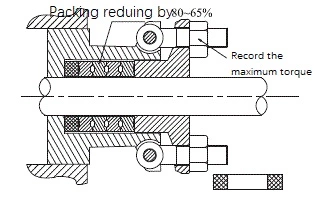
Figure 5 Packing Installation Step 3
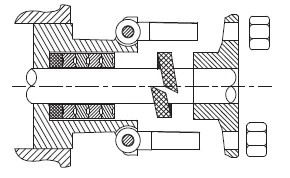
Figure 6 Packing Installation Step 4
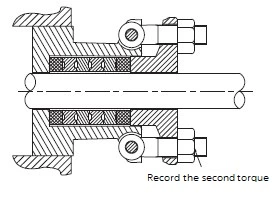
Figure 7 Packing Installation Step 5
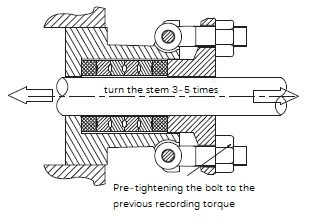
Fig. 8 Packing Installation Step 6
Conclusion
In fact, from the aspects of packing box design, packing selection and packing installation method, this paper analyzes the causes of valve stem sealing packing leakage and formulates specific solutions to ensure the quality of pipeline ball valves. The leakage of valve stem packing was sealed and good results were obtained. Appropriate packing materials should be selected according to different working conditions to achieve an effective sealing effect on the valve stem. The depth of the packing box and the diameter of the valve stem should be designed reasonably, and an appropriate packing sealing structure should be selected.