The
nodular cast iron pipe fittings include tees, elbows, couplings (such as socket types), etc. Their interfaces include socket, flange, etc. Nominal caliber ranges from DN80 to DN3000, and there are more than 5,000 kinds of commonly used varieties and specifications. Orders are usually in the form of multi-variety and multi-specification collocation. The production organization adopts a multi-specification collinear production mode, and the spare parts need to be machined.
The process is divided into two parts:
1. Turning the excircle, end face and inner hole of each interface;
2. Drilling flange holes. There are few special machine tools for pipe fitting processing in the market, so ordinary machine tools can only be used for processing, such as ordinary horizontal lathe, vertical lathe, T611 boring machine, rocker drill, etc., supplemented by a large number of fixtures, drills and another tooling.
There are the following problems in processing:
1. Common machine tools and tooling have poor versatility and limited adjustable range, which makes it difficult to meet the card loading requirements for multi-specification and multi-variety collinear production;
2. There are many processing parts of a single pipe fitting. The processing allowance of a single part is small, and the required processing time is short, but the clamping time is long, which affects the overall processing efficiency;
3. The use of ordinary machine tools requires a lot of labor, and the labor cost is getting higher and higher, so the quality is easily affected by labor and fluctuates.
To solve the above problems, it is necessary to optimize the processing technology, improve the processing tools, and even transform the equipment and customize the special processing machine tools. In this respect, few professional equipment manufacturers develop special tooling and equipment for pipe fittings, usually relying on pipe fittings factories to explore and improve themselves, so the development ability is limited; However, the development of special machine tools can't be done by small machine tool factories, and big factories are unwilling to do it. Our company has been producing pipe fittings for many years and has made many attempts in equipment modification, design and manufacture of special planes. Especially in recent years, with the application of numerical control technology, numerical control special machine tools have been popularized. This article mainly discusses the processing of small-sized pipe fittings within DN300.
Characteristics of DN80-DN300 Pipe Fittings
1. Although the nominal diameter of the products in this specification section is small, there are many demands, so the processing requirements are fast and efficient. Because the blank is usually produced in batch by production line, the product size is stable, and the socket and socket joints are usually cast directly. Only the flange face and the bolt hole (sand casting) need to be processed. In the EPC process, bolt holes are usually cast out, and some manufacturers even cast the flange end face directly.
2. The product has high shape consistency, so it is convenient to adopt a unified processing tool, and realize rapid positioning, hydraulic clamping and numerical control automatic processing by using rough benchmark positioning of the blank.
3. The quality of these products is between 8 and 25 kg. They are light, so they can be handled by hand.
Processing Technology Analysis
According to different blank casting processes of products with specifications below DN300, the machining allowance of pipe fittings is usually different, and there are usually the following three different practices.
1. The socket of pipe fittings is cast and formed, and the flange needs to be processed, including turning the flange surface and drilling the flange hole. Usually, the products cast by sand mold belong this way. As shown in Figure 1.
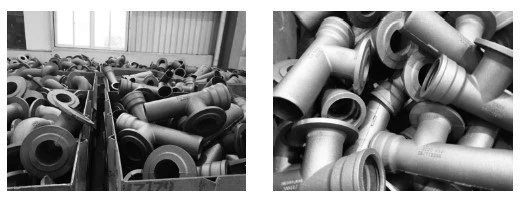
Fig. 1 DN100~DN300 pipe fittings blank
2. The socket of pipe fittings is cast, and the flange hole is cast as a whole. Only the flange end face needs to be processed. This is usually used in the EPC process.
3. The socket and the flange of pipe fittings are all cast, including the flange face and flange hole. Only some pipe fittings which do not meet the size requirements due to shrinkage fluctuation and out-of-round are processed. The processing quantity depends on the stability of the casting process.
The configuration and processing of machine tools are discussed in the first case below, and those mentioned above second and third types can be selected and used in the third type of processing machine tools. According to the above analysis, the main processing contents of small pipe fittings are the turning surface and drilling of the flange. The processing technology needs to be designed separately for different types of pipe fittings.
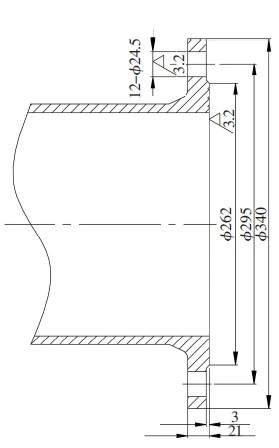
Fig. 2 DN200 flange processing drawing
The processing parts of pipe fittings with the disc are usually the sealing surface of the flange and the bolt hole of the flange. Processing requirements are shown in Figure 2. It is usually divided into two processes: turning (or boring) and drilling. The first working procedure: the end face of the flange is processed by a boring machine or lathe. YG6 and YG8 cemented carbide cutters are used, with a linear speed of 80 m/min and a feed rate of 0.10 ~ 0.15 mm/r; The second working procedure: the bolt hole is processed with a rocker drill or a multi-hole drill, and the ordinary twist drill or alloy drill is used for dry cutting. The processing effect of the above products can meet the requirements of surface roughness Ra6.3 μm and dimensional tolerance.
Because each flange interface needs to be processed one by one. Even if there is only one flange on a pipe fitting, it needs two processes and two clamping times. Because of multi-specification collinear production, it is necessary to frequently adjust the fixture when the specification changes, so as to ensure that all specifications of products on duty flow at the same time.
For parts with multiple flanges, it is necessary to process the flanges one by one and repeat the same processing for other interfaces to form a finished product. For example, a three-plate tee joint requires three turning and three drilling times, and a total of six loading and unloading times. The branch pipes of flange parts on tee parts are also different in size, and there are few batches, so the adjustment of processing tools is more frequent.
In order to improve the efficiency, according to the characteristics of the above-mentioned pipe fittings, it is advisable to adopt the method of simultaneous processing of multiple parts or single part and multiple processes combined in one clamping, so as to reduce the auxiliary time of clamping and positioning of workpieces and the number of clamping, which is the key to improve the processing efficiency.
Types of Processing Equipment
According to the number and position of flanges, we divide the products into single flange parts and multi-flange parts according to the number of parts to be processed. If only one flange of a pipe fitting needs to be processed, we call it a single flange piece, and the products include disk bearings, disk inserts, tees with supporting disks, etc. If there are two or more flanges on a single pipe fitting, it is called a multi-flange pipe fitting, including a double-disc short pipe, double-disc elbow, double-disc reducer, three-disc tee, etc.
1. Processing technology and equipment scheme of single flange pipe fittings
Its processing technology is preferred to adopt the method of turning and drilling in one, and all the processing can be completed by loading the card once. As shown in Figure 3, this machine tool is equipped with a boring head and a group of drill bits, which are installed on a power sliding table and brought back to a rotary table. It is equipped with four stations, one loading and unloading station, one boring station and one drilling station, and one station is reserved. Two powerheads are sequentially arranged at the boring station and the drilling station. After the rotary table finishes processing one interface, it turns 90° to enter the next process, and so on. The three working procedures of card loading, turning and drilling can work at the same time, and the efficiency is doubled.
If the hole has been cast in the blank, only the flange surface needs to be machined. One drilling powerhead can be stopped, and a single powerhead can be used. The comparison with the processing efficiency of common machine tools is shown in Table 1.
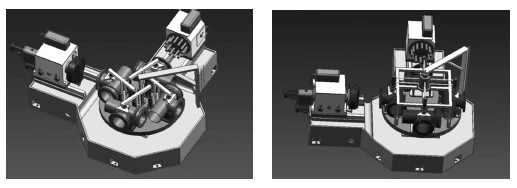
Figure 3 Rotary desktop CNC special machine tool
Table 1 Comparison of processing efficiency of single flange pipe fittings
project |
General e tool scheme |
Rotary table special machine tool scheme |
Comparison |
turning |
drilling |
total |
turning/ drilling |
total |
Machining process |
√ |
√ |
2 processes |
turning and drilling at the same time |
1 process |
none |
Processing equipment |
boring machine/lathe |
group drilling |
twice clamping |
turning and drilling integrated |
once clamping |
one clamping reduction |
The processing time per piece/min |
2 |
1 |
3 |
1 |
1 |
The efficiency is three times of
general machines |
2. Processing technology and equipment scheme of multi-flange pipe fittings
This kind of pipe fitting has two or more flanges to be machined on a single pipe fitting. The products include three-disc tees, two-disc short pipes, two-disc 90° elbows, two-disc reducers and other pipe fittings. Each flange also needs two processes turning and drilling. If the above rotary desktop bed is used for processing, it still needs to be processed many times, and the overall efficiency will be reduced. If ordinary machine tools are used for processing, it needs two processes for each surface, and the efficiency is low.
After optimization, the multi-side simultaneous machining process is adopted, which is divided into two processes: multi-side simultaneous turning and multi-side simultaneous drilling. Each process is carried out on a different machine, and two pieces of equipment are combined to form a machining unit. The process connection can be realized by a manipulator or manually. Although twice processing is required, the overall efficiency is still better than that of single-disk machine tools because 2 or 3 surfaces can be processed at the same time, and only one interface time is needed.
This machine draws lessons from the structure of a special machine tool for valve processing. As shown in Figure 4, the special machine tool for three-sided boring is equipped with three boring powerheads, which are controlled by separate numerical control systems, and can process interfaces of different sizes and specifications respectively. The three-sided drilling machine is shown in Figure 5. Three groups of drill bits are arranged vertically with each other and controlled by the numerical control system, which can realize simultaneous processing of three interfaces. The above-mentioned three-sided special machine tool can work independently with three heads to process workpieces of different sizes and shapes, so as to adapt to the processing of pipe fittings with different specifications and different interfaces of main pipes and branch pipes. At the same time, it is equipped with a special fixture to realize quick positioning and automatic clamping. Only loading and unloading are required, and the numerical control of the machining process is automatically completed. Because the workpiece is light, loading and unloading can be done manually. If the unmanned operation is required, a manipulator can be equipped to load and unload two machine tools.
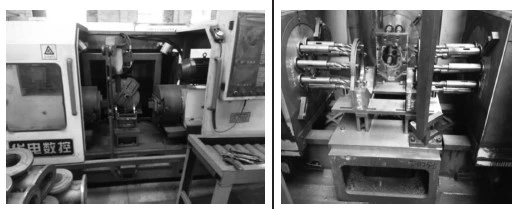
Figure 4 on the left: Three-sided boring machine
Figure 5 on the right: Three-sided drilling machine
Compared with ordinary machine tools, the efficiency is greatly improved, especially the three-disc and three-links. Table 2 compares the processing efficiency by taking the processing of three discs and three tees as an example.
Table 2 Comparison Table of Processing Efficiency of Multi-flange Pipe Fittings
Project |
General Machine Tool Scheme |
Multi-head Special Machine Tool Scheme |
Comparison |
turning machines |
drilling machines |
total |
boring machines |
drilling machines |
total |
Machining process |
car 1-car 2- car 3 |
Turning face 1-drilling face 2- drilling face 3 |
6 processes |
3-face boring |
3-face drilling simultaneously |
2 processes |
none |
Machining equipment |
boring machine/lathe |
group drilling |
6 times loading |
three-sided boring machines |
three-sided group drilling |
2 times clamping |
reduce 4 times clamping |
Single piece processing time
/min |
2×3 |
1×3 |
9 |
1 |
1 |
2 |
reduced by 7 min/ piece, and the efficiency is 4.5 times of the original. |
The above-mentioned special machine can also be used for processing two interfaces and single-plate products because the three powerheads can be controlled independently, and the efficiency advantage will be reduced. However, when the specifications of pipe fittings are concentrated, multiple machines can process the same specification at the same time, thus improving the adaptability of the machine tool.
3. Processing technology and equipment scheme of pipe fittings with multiple interfaces that need to be processed at the same time.
There is another situation in the above-mentioned pipe fitting process. There are more than two interfaces on the same pipe fitting, and each interface is different in size and form. All of them need to be machined, such as socket elbows and socket single-branch tees. If all interfaces need to be machined, although the above two kinds of equipment can be machined one by one, the time-consuming effect of card loading will obviously increase, so another machine tool is needed for machining. It's the only way to finish multi-surface machining by loading cards at one time for multi-interface parts. However, when the specifications and types of multi-surface parts are different, it's necessary to use CNC single-power lathe with rotary tables. This machine tool mainly solves the problem of multi-sided processing with one card loading, and reduces the auxiliary time of card loading, as shown in Figure 6.
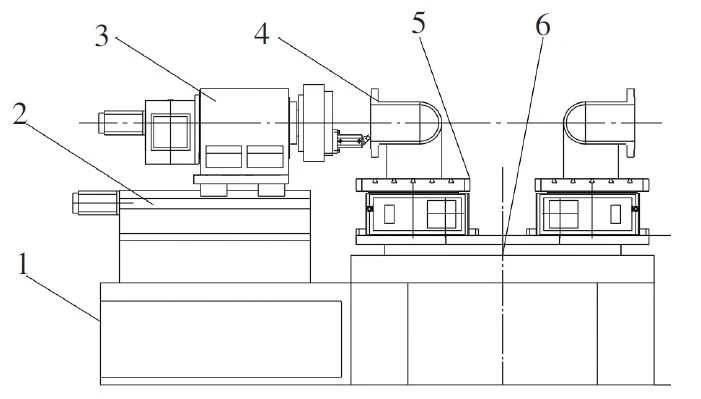
Figure 6 Single-head rotary desktop special plane
1. a base; 2. power sliding table; 3. boring head; 4. workbench; 5. multi-station small turntable; 6. two-station rotation
The combination of the boring headstock and sliding table realizes automatic processing of the flange end face, socket outer circle and end face, socket inner hole and end face under the control of a numerical control system. One interface is processed each time. After processing, table 4 is rotated by a set angle according to the program set to realize the second interface. In this way, after the complete pipe fitting is processed, the two-station workbench shown in Figure 6 is rotated by 180°, and the workpiece is to be processed and the processed workpiece is exchanged. The operator side performs the next operation, and the powerhead side automatically starts processing. It realizes card loading and processing at the same time and completes all interfaces at one time.
Conclusion
According to the characteristics of small pipe fittings, the pipe fittings produced by multi-varieties and small batches in the same line are classified according to the processing characteristics. The processing technology is optimized by means of process merging, multi-station simultaneous processing, etc. The efficiency is improved and the quality is stable by using special numerical control machine tools. One person can operate two or more machines, realizing the batch processing of pipe fittings. The design of special machine tools can be done by pipe fitting factory's own design and manufacture, or by cooperation with machine tool factory. However, the processing technology needs to be designed and put forward by the pipe fitting factory itself, so that it is possible to find a special machine developed by professional equipment manufacturers in cooperation, so as to improve the automation level of pipe fitting processing equipment and promote the development of pipe fitting industry.