Liquefied natural gas (LNG) receiving station is an important part of China's LNG storage and transportation equipment system, and the cryogenic butterfly valve is the key equipment to ensure the safe and reliable operation of the pipeline system of the receiving station. The requirement of hazardous gas emission in LNG tank farm makes flange-connected ultra-low temperature butterfly valve unacceptable, and butt-welded ultra-low temperature butterfly valve has become the first choice for design institutes and users. In this paper, the valve body, seal and other structures of several typical ultra-low temperature butterfly valves are analyzed, providing a reference for users to choose ultra-low temperature butterfly valves.
Valve body structure
1. Ordinary butt welding ultra-low temperature butterfly valve
As shown in Figure 1, the ordinary butt-welding ultra-low temperature butterfly valve changes the flange connection to the butt-welding connection and adopts a welding connection with the pipeline, which completely eliminates the possibility of leakage at the flange bolt connection seal. If the sealing pair of ordinary butt-welding ultra-low temperature butterfly valve is damaged, the whole valve can only be cut and the sealing parts or the whole valve can be replaced during maintenance. The maintenance operation of ordinary butt-welding ultra-low temperature butterfly valves will not only cause potential safety hazards in LNG tank farms (sparks generated by cutting and welding) but also require the system to be shut down for a long time, resulting in huge cost waste.
2. Butt welding side is equipped with an ultra-low temperature butterfly valve.
The connection mode between the ultra-low temperature butterfly valve installed at the butt welding side and the pipeline butt welding remains unchanged, and an access opening is provided at one side of the valve body. Butt welding side mounted ultra-low temperature butterfly valve is divided into two kinds of structures, one is that the valve seat is an integral cemented carbide surfacing structure, and the sealing ring can be replaced (Figure 2); The other is that the whole set of sealing pairs of the valve seat and sealing ring can be returned (Figure 3). During the system's regular operation, the sealing between the maintenance valve cover and the valve body is guaranteed by bolt connection; When the system is stopped for maintenance, open the maintenance valve cover for maintenance, and replace the valve seat or sealing ring. Compared with ordinary butt-welded ultra-low temperature butterfly valves, the butt-welded side-mounted ultra-low temperature butterfly valve avoids dangerous operations on LNG tank farms. The disadvantages are that the opening of the access port lengthens the length of the valve structure, and the installation of a replaceable valve seat and butterfly sealing ring leads to complicated valve structure design and increases the valve cost. Due to the limitation of the maintenance space of the valve body, the small diameter (below DN500) butterfly valve is not conducive to the extension and flexion of the maintenance staff's arms, and the on-site maintenance and overhaul work is not easy to carry out.
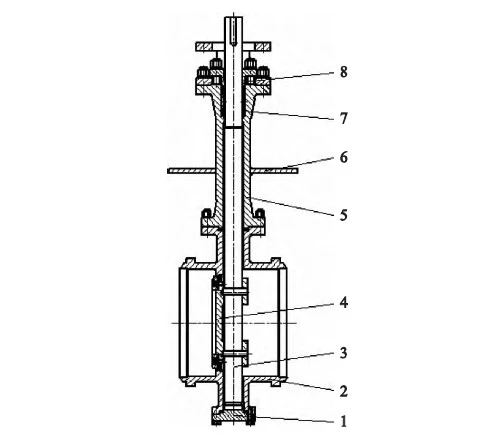
1. End cover 2. Butt-welded valve body 3. Valve stem 4. Butterfly plate assembly
5. Low-temperature extension pipe 6. Drip tray 7. Packing 8. Packing gland.
Figure 1 Ordinary Butt Welding Ultra-low Temperature Butterfly Valve
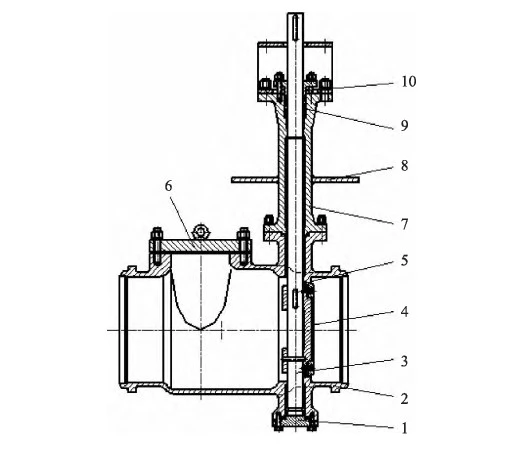
1. End cover 2. Side-mounted valve body 3. Valve stem 4. Butterfly plate assembly 5. Integral valve seat
6. Side valve cover 7. Low-temperature extension pipe 8. Drip tray 9. Packing 10. Packing gland.
Figure 2 Integral valve seat butt welding side mounted ultra-low temperature butterfly valve
Install ultra-low temperature butterfly valve for butt welding.
The ultra-low temperature butterfly valve (Figure 4) is installed in butt welding to connect with the pipeline, and an access opening is set in the middle cavity. The structural sealing ring can be replaced. The sealing ring, butterfly plate and pressure plate are fixed by bolts, and the valve seat is cemented carbide surfacing of the whole valve body. On-site maintenance directly opens the valve cover, lifts the butterfly plate, valve stem, valve cover, low-temperature extension pipe and actuator as a whole, and repairs or replaces the sealing parts. As the valves are distributed all over the pipeline, it is difficult to lift them on site, especially for butterfly valves with specifications above DN600. Mounting an ultra-low temperature butterfly valve is a beneficial supplement to a small diameter side-mounted ultra-low temperature butterfly valve.
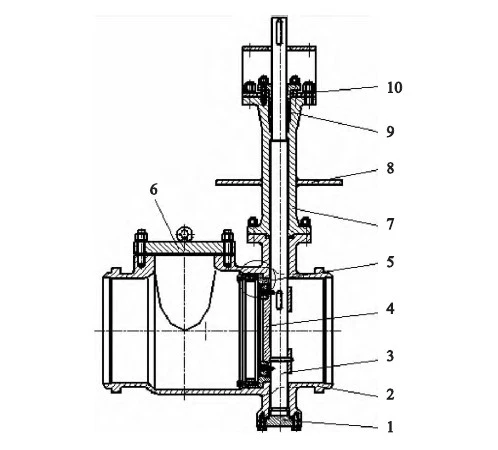
1. End cover 2. Side-mounted valve body 3. Valve stem 4. Butterfly plate assembly 5. Replaceable valve seat
6. Side valve cover 7. Low-temperature extension pipe 8. Drip tray 9. Packing 10. Packing gland.
Figure 3 Replaceable valve seat butt welding side mounted ultra-low temperature butterfly valve
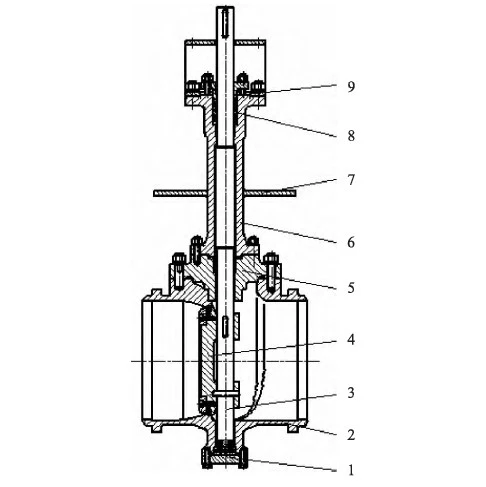
1. End cover 2. Upper valve body 3. Valve stem 4. Butterfly plate assembly 5. Upper valve cover.
6. Low-temperature extension pipe 7. Drip tray 8. Packing 9. Packing gland.
Fig. 4 Ultra-low temperature butterfly valve for butt welding
Sealing Structure
An LNG butterfly valve is divided into a double eccentric sealing structure and a triple eccentric sealing structure according to the sealing principle of a butterfly valve.
Double eccentric sealing structure
The double eccentric sealing structure is shown in Figure 5, in which the structure (A) cannot meet the fire protection requirements of the LNG ultra-low temperature butterfly valve. The valve seat sealing ring with a double eccentric sealing structure can be replaced, and the butterfly plate is of integral structure. Its principle is to reduce the friction between the butterfly plate sealing surface and the valve seat sealing ring in the opening and closing process by means of the two eccentricities of the valve stem rotation center, the valve seat sealing ring center and the pipeline center. With the help of the elastic valve seat sealing ring, the resilience of the spring and the pressure difference of the medium, the sealing pairs are more closely matched to ensure the reliability of sealing. Double eccentric sealing structure, its valve seat sealing ring has good compatibility, easy replacement, and low technical requirements for operators. However, in the process of valve opening and closing, the butterfly plate will rub against the valve seat, the sealing ring will be easily damaged, and the maintenance period will be short. Generally, the elastic sealing ring is made of nickel alloy, which is expensive and difficult to process. When the butterfly sealing surface is damaged, the butterfly valve needs to be completely replaced if it cannot be repaired on-site.
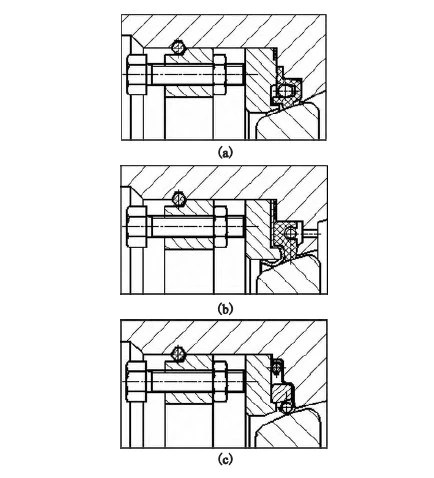
(a) Non-metallic elastic sealing ring (b) Non-metallic elastic sealing ring+fireproof sealing ring
(c) Metal elastic sealing ring
Figure 5 Double eccentric seal structure
Triple eccentric sealing structure
As shown in Figure 6, the triple eccentric sealing structure can be divided into integral valve seat structure and replaceable valve seat structure, and the sealing ring can be replaced. The principle is that by means of the two eccentricities of the rotation center of the valve stem, the center of the sealing ring of the valve seat and the center of the pipeline, and the angular eccentricity, the sealing ring and the sealing surface of the valve seat have no interference and friction in the whole process of valve opening and closing. In addition, the valve seal mainly depends on the torque of the valve stem and the grinding mechanism of the closing stroke.
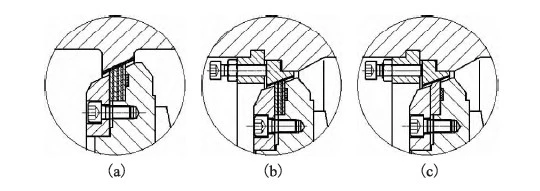
(a) integral valve seat and replaceable multi-layer sealing ring (b) replaceable valve seat and multi-layer sealing ring.
(c) Replaceable valve seat and all-metal sealing ring
Fig. 6 Triple eccentric sealing structure
The valve with a triple eccentric sealing structure has no friction in the whole opening and closing process, the sealing ring is not easily damaged, the service life is long, and the valve seat or sealing ring can be replaced. The metal sealing structure has fireproof performance. However, the triple eccentric sealing structure has high requirements for the matching and positioning of the valve seat and sealing ring, so the maintenance and replacement need professional technicians.
Analysis of fugitive seal structure
The application design of ultra-low temperature butterfly valve in LNG cryogenic conditions, from double flanges to butt welding, to the design of an online repairable butt welding valve body, is essential to reduce the risk of fugitive leakage and improve the safety and convenience of the whole cycle. The connection between the valve and the pipeline is a kind of flexible connection. Because of the superposition of temperature, pipeline deformation stress and docking with the dock of an LNG carrier, it is easy to cause the relative displacement of the connecting flange, which leads to the leakage of the flange seal. The static sealing connection between the valve body and bonnet, valve body and end cover of the low-temperature butterfly valve belongs to a rigid connection, which is not affected by an external force, and there is no sealing leakage caused by relative displacement caused by stress.
According to ISO15848-1 and "Domestic Development of Key Valves for Liquefied Natural Gas-Test Program of Cryogenic Butterfly Valve", the allowable leakage rate at the joint between the valve body and valve cover (the leakage per millimeter of gasket circumference at the joint between the valve body and valve cover) is ≤ 1. 78× 10-8pa m3/s, and the allowable leakage rate at the valve stem packing seal (the leakage per millimeter of valve stem diameter at the measuring point). The dissipation requirement of the static seal is much higher than that of a dynamic seal, and the static seal is easier to meet the standard requirements than the dynamic seal. And static sealing positions such as valve body, valve cover, valve body and end cover, etc., it is easier to meet the standard requirements by selecting sealing materials and improving sealing force.
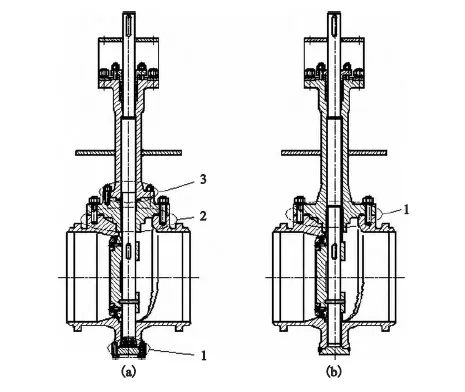
(a) Split type (b) Integral type
Figure 7 Structure of extended bonnet
The structure of the extended bonnet is shown in Figure 7, in which there are three static seal leakage points and one dynamic seal leakage point of the split extended bonnet. The split design divides the valve cover and the extension pipe into two parts, which increases the number of parts, has a simple structure and is easy to process. There are two leakage points of the static seal and one leakage point of the dynamic seal of the integrally extended bonnet. After the end cover is welded with the valve body, the leakage point of the static seal can be reduced to one. The integral design combines the valve cover and the extension pipe into a whole, which makes the shape of the casting complex and increases the casting difficulty. Welding the end cover with the valve body is not conducive to the precise positioning of the butterfly plate and the disassembly of the valve stem. And the risks of dissipation and safety are reduced. The leakage risk of valve dissipation is inevitable, so the structural design should take into account the user requirements and process.
Conclusion
In this paper, the valve body structures of common butt-welding ultra-low temperature butterfly valve, butt-welding side-mounted ultra-low temperature butterfly valve and butt-welding top-mounted ultra-low temperature butterfly valve are introduced, and the double eccentric and triple eccentric sealing structures are compared and expounded. Finally, the dissipation requirements of the LNG ultra-low temperature butterfly valves are analyzed. When selecting an LNG ultra-low temperature butterfly valve, careful analysis and comparison should be made according to the working conditions and the specific requirements of the pipeline system, and appropriate products should be selected, so that the products can meet the service performance of working conditions to the maximum extent.