For a long time, process manufacturers have been pursuing the goal of predictive maintenance by deploying device monitoring systems to anticipate potential equipment failures while allowing healthy equipment to continue operating. Achieving this goal can significantly reduce maintenance costs for production enterprises and effectively prevent unexpected power outages and downtime. In theory, every company should adopt this predictive maintenance approach, but few can achieve this goal because predicting the future poses many challenges in practical operation. This article will introduce some diagnostic and data processing measures for predictive maintenance. These measures have been put into practice and have achieved certain results in the
automation valve industry, and are under continuous development and updating.
1. Proactive Maintenance vs Reactive Maintenance
Automatic control valves are critical components in the process industry, and unexpected failures can result in millions of dollars in losses annually. When automatic control valves are set to automatic mode (which is usually the case), the controller compensates for declining valve performance, allowing the circuit to continue operating even when valve performance is degraded, until the valve eventually fails completely, disrupting the process or forcing a shutdown. Throughout this process, automatic control valves do not provide clear warning information.
In fact, there are always signs of impending failure, although these signs may be very subtle (figure 1). If these signals can be detected and acted upon, components needing repair can be identified promptly, and brief shutdowns or bypasses can be arranged for maintenance, minimizing production losses caused by unexpected accidents.
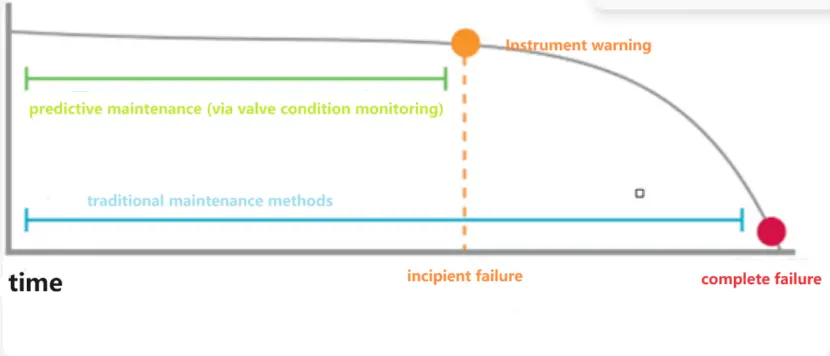
Figure 1: proactive valve maintenance VS reactive maintenance
The key factor in achieving predictive maintenance is data; the more data you have, the more accurate the predictions. Traditional automated valves only collect valve position data and cannot provide other necessary data. With the development of intelligent diagnostic digital valve controllers, more and more data can be obtained. These digital valve controllers monitor valve operation and detect abnormalities through a series of sensors. Some high-end controllers allow for both offline and online monitoring, capturing initial installation data and comparing it with operational data, recording differences. This online monitoring can capture valve performance data and some transient issues during operation, which are difficult to achieve under traditional circumstances.
2. Value Lies in Utilized Data
Data is crucial for achieving predictive maintenance. Only when professional expertise receives and professionally evaluates this data can comparatively accurate predictive results be obtained. The entire process is primarily hindered by the following issues:
(1) Installed valve controllers may be old models lacking the ability to monitor and capture necessary data.
(2) Digital valve controllers can capture data, but they cannot transmit this data; technicians must come to the site to obtain the data.
(3) Digital valve controllers are connected to maintenance networks and transmit data to public locations, but relevant personnel lack the necessary knowledge and experience to properly interpret this data and draw actionable conclusions.
Hardware Investment
The first issue will be resolved over time. As old valve controllers fail, most users will replace them with new intelligent digital valve controllers. These valve controllers employ advanced sensors and communication technologies, with different performance levels; high-end products can provide shutdown detection, operational diagnostics, and partial stroke testing.
If companies want to achieve predictive maintenance, they need to invest more in digital valve controllers, including in-service valves and newly installed valves, especially those critical valves operating under harsh conditions that are crucial to production. The improvement in diagnostic capabilities, reduction in maintenance costs, and increase in normal operating time enable the investment in digital valve controllers to pay off in a short period.
Data Transmission
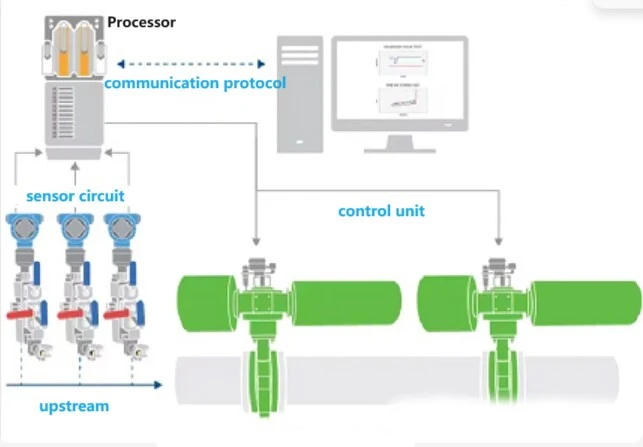
Figure 2: valve data collection and transmission
The second issue concerns data transmission, which has been effectively addressed with the development of information and communication technologies. New intelligent digital valve controllers can transmit data through wired or wireless communication protocols (figure 2). Only through real-time continuous access and monitoring of data is predictive maintenance possible. Enterprises extract data through control systems and transmit it to accessible public locations or other designated locations.
Remote Expertise
The most challenging aspect of achieving predictive maintenance is finding professional expertise. Professional expertise can professionally evaluate captured data, diagnose occurring issues, and take appropriate actions to address them, preempting valve failures. Currently, some large companies have solutions, and more solutions are under development. For example, the Fisher FIELDVUE ValveLink software system can automatically perform scheduled online diagnostics while the valve is in operation, continuously monitor pressure, performance degradation, and packing issues, and provide alerts. Future software may use applications with built-in machine learning and artificial intelligence to identify emerging issues and propose solutions.
If a factory lacks professional expertise in monitoring valve information, it can securely transmit data to remote experts with extensive experience who can act as extensions of on-site personnel. Experts can communicate long-term issues and immediate concerns to factory personnel (figure 3). This remote service can monitor valve performance degradation and predict impending failures before valve failures occur, effectively alleviating the pressure on production personnel. It also provides factory personnel with an opportunity for continuous consultation and communication with valve experts regarding performance and improvement measures.

Figure 3: Remote think tank monitoring and analysis service solution
3. Return on Data Investment
A herbicide factory transitioned from reactive maintenance to predictive maintenance using advanced control valve diagnostic technology, resulting in a yearly reduction of $230,000 in maintenance costs. In one practical case, the factory identified a problematic control valve through monitoring and took preventive maintenance before the valve failed completely, saving nearly $100,000.
A refinery found that 26 critical valves in its hydrocracking unit could potentially cause unexpected shutdowns. However, lacking valve expertise, the refinery hired valve suppliers to provide remote services for continuous monitoring and reporting of these valves. The expertise detected a large anti-surge valve leak and several heating valves with issues. Using this information, repairs were conducted without shutdowns, avoiding a $5.6 million unplanned shutdown and saving $400,000 annually by improving the performance of heating units.
4. Seizing the Future
Predicting the future is not easy, but when necessary data can be collected and transmitted to professional expertise, predicting the future becomes possible. With the development of digital valve controllers, the next generation of digital valve controllers will be able to collect and provide more data. Capturing and transmitting this data to the right locations and processing it through advanced software and remote expertise can transform this data into actionable insights, enabling predictive maintenance and preventing complete failures. New communication technologies such as Ethernet APL and local real-time control enable the rapid development of digital valve controllers, continuously improving predictive accuracy, reducing maintenance costs, and increasing normal operating time. Upgrading equipment intelligence, combined with remote expert services when necessary, will bring significant returns to enterprises in the future. Moreover, as time progresses, their performance will continue to improve, making predictive maintenance feasible.